URGE Designs Ohlins Lower Cup Review
#11

Machining quality looks very nice on these! Looking forward to seeing the final product. From my standpoint, the closest you can get it to looking like it came from the Ohlins factory the better. How hard is it to get some new DFV labels? :P
#13

Subd for more info on the release of these.
PS I'm not a suspension guru, I just have an engineering background and this is what I can deduce from the available info.
Last edited by V3rtigo; 04-18-2017 at 06:29 PM.
#14
Registered User


The stock ohlins cups and normal dampers typically have steel mounting points to control arms that if some type of minor impact occurs will bend vs crack. Can you speak to the machined cups ability to not shear or crack at the mounting points? I always worry about having certain suspension pieces crack instead of bench if you have an off or drop a wheel etc.
#15

Great question. That is EXACTLY why we choose 7075 Aluminum vs 6160. It has almost 2X the fatigue life of 6160 and almost 2X the shear strength of 6160.
As you noted, for suspension mounts, it is much more appropriate than typical aluminum and due to thickness, inline and even stronger than Steel.
As you noted, for suspension mounts, it is much more appropriate than typical aluminum and due to thickness, inline and even stronger than Steel.
The following users liked this post:
Dezoris (04-29-2017)
#16

Speed6 has the prototype and thus anodized.
The final product will be anodized for sure.
As you can see our manufacture really made a clean looking well designed product.
We opted to go with a ~2X stronger and ~2X higher fatigue life 7075 vs 6160 as the original part had steel mounts. We feel that is important for a part the has so much stress on it.
URGE
The final product will be anodized for sure.
As you can see our manufacture really made a clean looking well designed product.
We opted to go with a ~2X stronger and ~2X higher fatigue life 7075 vs 6160 as the original part had steel mounts. We feel that is important for a part the has so much stress on it.
URGE
Not that 7075-T6 is a bad alloy, I quite like it, but more fatigue performance usually isn't a driver on an automotive application where it's better just to refine the design or toss a few more grams of material at it to lower the stress.
If you want to tout the benefits of 7075-T6, I'd stress that the higher hardness vs. 6061-T6 makes it more suitable for a threaded part, since cosmetic anodizing (Type II) doesn't really provide much protection for that.
#17

While 7075-T6 is quite a bit stronger to yield than 6061-T6, the fatigue life for high cycle fatigue (what this design would only ever fail from in normal usage) is not anywhere close to 2x the 6061-T6 baseline. It might be 20% higher at high cycle numbers, but probably not even that depending on how many cycles.
Not that 7075-T6 is a bad alloy, I quite like it, but more fatigue performance usually isn't a driver on an automotive application where it's better just to refine the design or toss a few more grams of material at it to lower the stress.
If you want to tout the benefits of 7075-T6, I'd stress that the higher hardness vs. 6061-T6 makes it more suitable for a threaded part, since cosmetic anodizing (Type II) doesn't really provide much protection for that.
Not that 7075-T6 is a bad alloy, I quite like it, but more fatigue performance usually isn't a driver on an automotive application where it's better just to refine the design or toss a few more grams of material at it to lower the stress.
If you want to tout the benefits of 7075-T6, I'd stress that the higher hardness vs. 6061-T6 makes it more suitable for a threaded part, since cosmetic anodizing (Type II) doesn't really provide much protection for that.
Fatigue Strength is 23K vs 14K PSI or about 64% higher.
Shear Strength is 48K vs 30K or 60% higher
Yield Strength is 73K vs 40K PSI or 80% higher
And as you noted the Brinell hardness is 150 vs 95.
So across the board, a much better alloy for suspension mounting.
#18

Careful - aluminum does not have a defined "fatigue strength" (termed an endurance limit). More cycles means less stress needed to generate a fatigue failure, so aluminums are typically not rated as having a fatigue strength. I know some places do it because people know the term, but it's just the strength at some number of cycles and the fatigue strength keeps dropping above that.
Shear is also not a consideration here, since this is not a slip joint once torqued (bolt preload generates enough joint friction to hold things together).
Fatigue is pretty complicated, but here's how these aluminum alloys perform:
7075-T6:
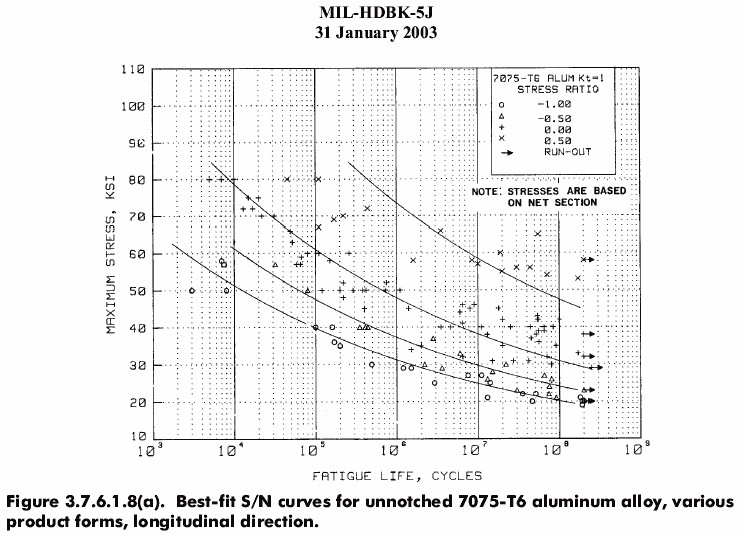
6061-T6:

7075 does have more strength at the same number of cycles as 6061, but given enough cycles, it will still drop down to where the 6061 was at an earlier number of cycles. It never "levels off" like say steel does around 10^6 to 10^7 cycles.
BTW - you guys might want to cross shop 2024-T3 as an alternative alloy. Sometimes it can be a little cheaper than 7075 in my experience, but has great fatigue performance and hardness.
I've personally seen failures due to people designing to a published "fatigue strength" on aluminum, and not taking into account more loading cycles over a part's lifetime.
Shear is also not a consideration here, since this is not a slip joint once torqued (bolt preload generates enough joint friction to hold things together).
Fatigue is pretty complicated, but here's how these aluminum alloys perform:
7075-T6:
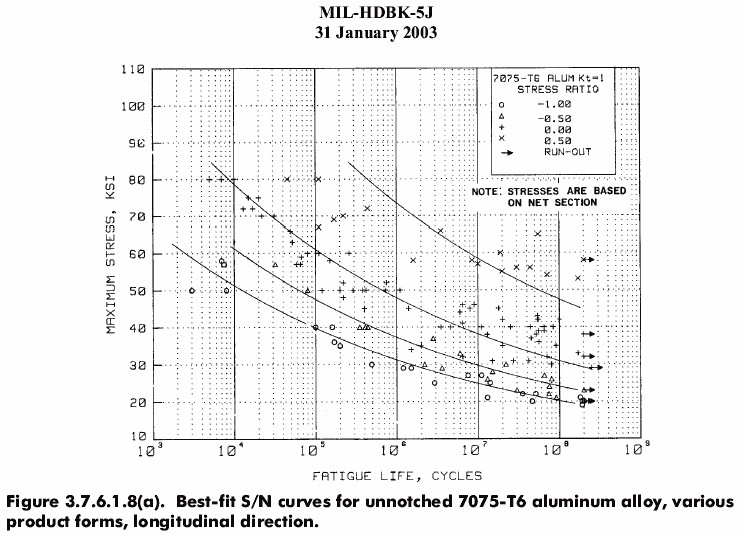
6061-T6:

7075 does have more strength at the same number of cycles as 6061, but given enough cycles, it will still drop down to where the 6061 was at an earlier number of cycles. It never "levels off" like say steel does around 10^6 to 10^7 cycles.
BTW - you guys might want to cross shop 2024-T3 as an alternative alloy. Sometimes it can be a little cheaper than 7075 in my experience, but has great fatigue performance and hardness.
I've personally seen failures due to people designing to a published "fatigue strength" on aluminum, and not taking into account more loading cycles over a part's lifetime.
#20

We could not match the Gold as anodization is difficult on 7075 Aluminum so we went with a dark grey.
We feel the 7075 Aluminum is worth it as is a much stronger aluminum than 6160, which is important for a suspension mount.
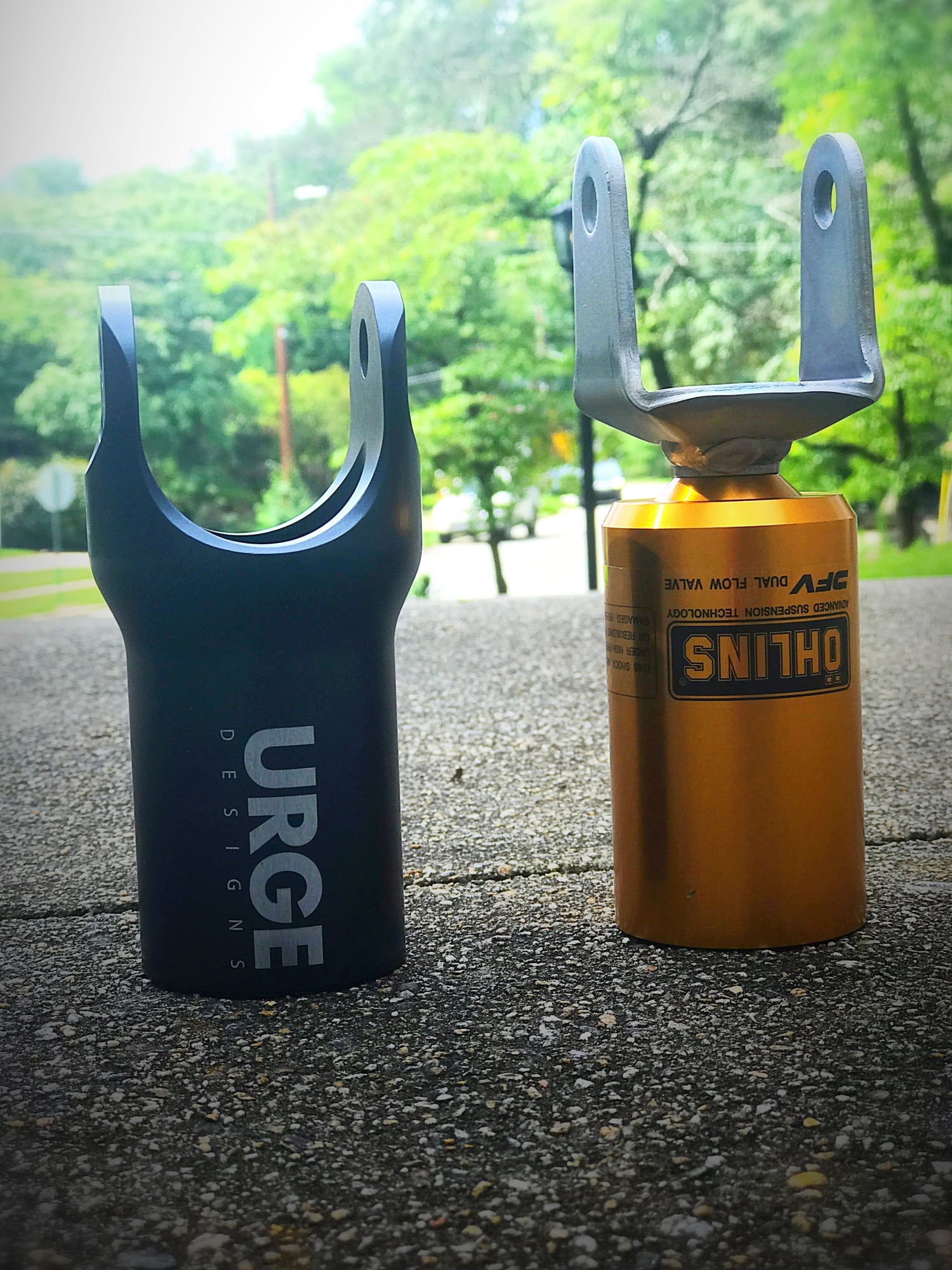
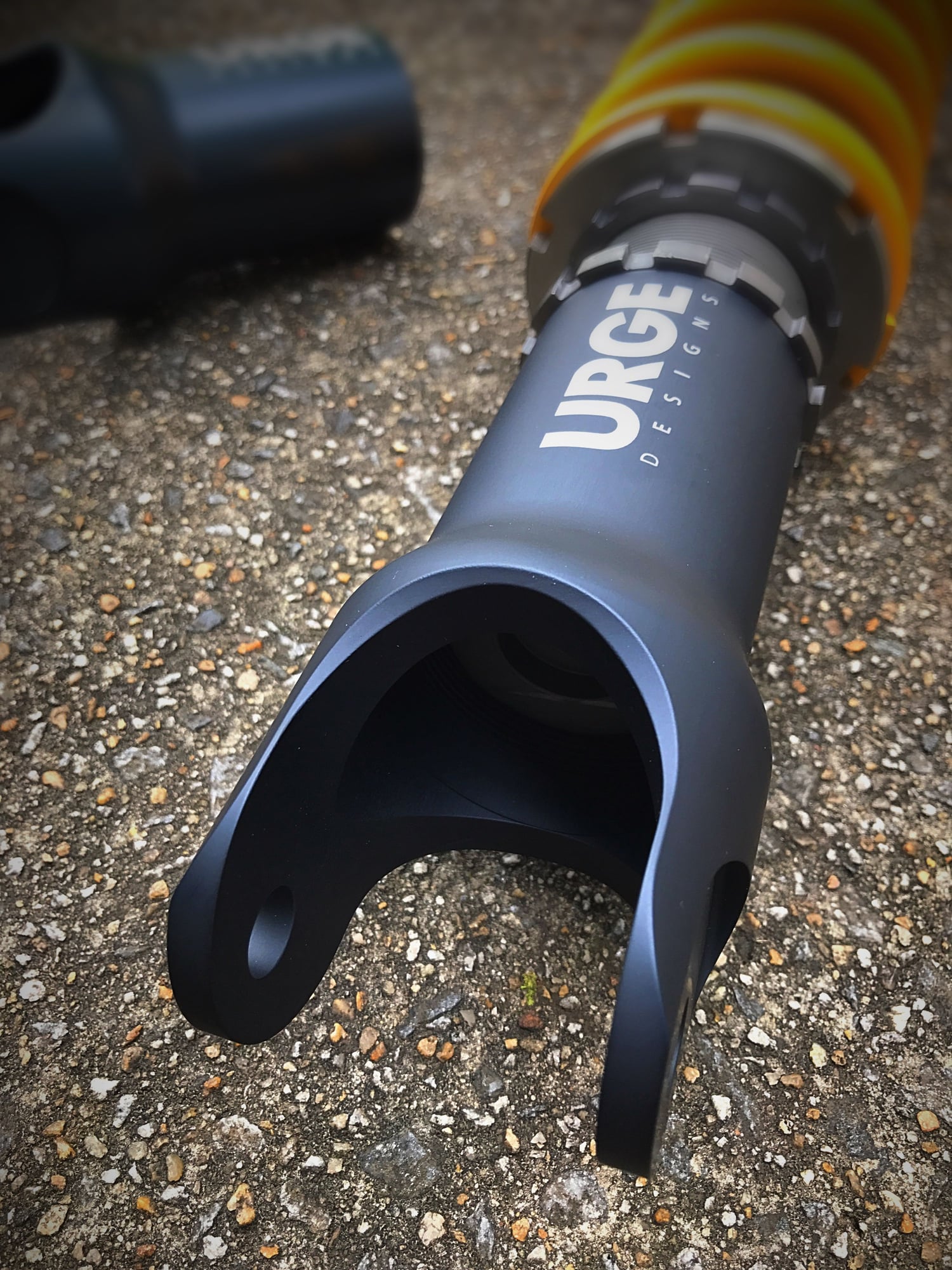
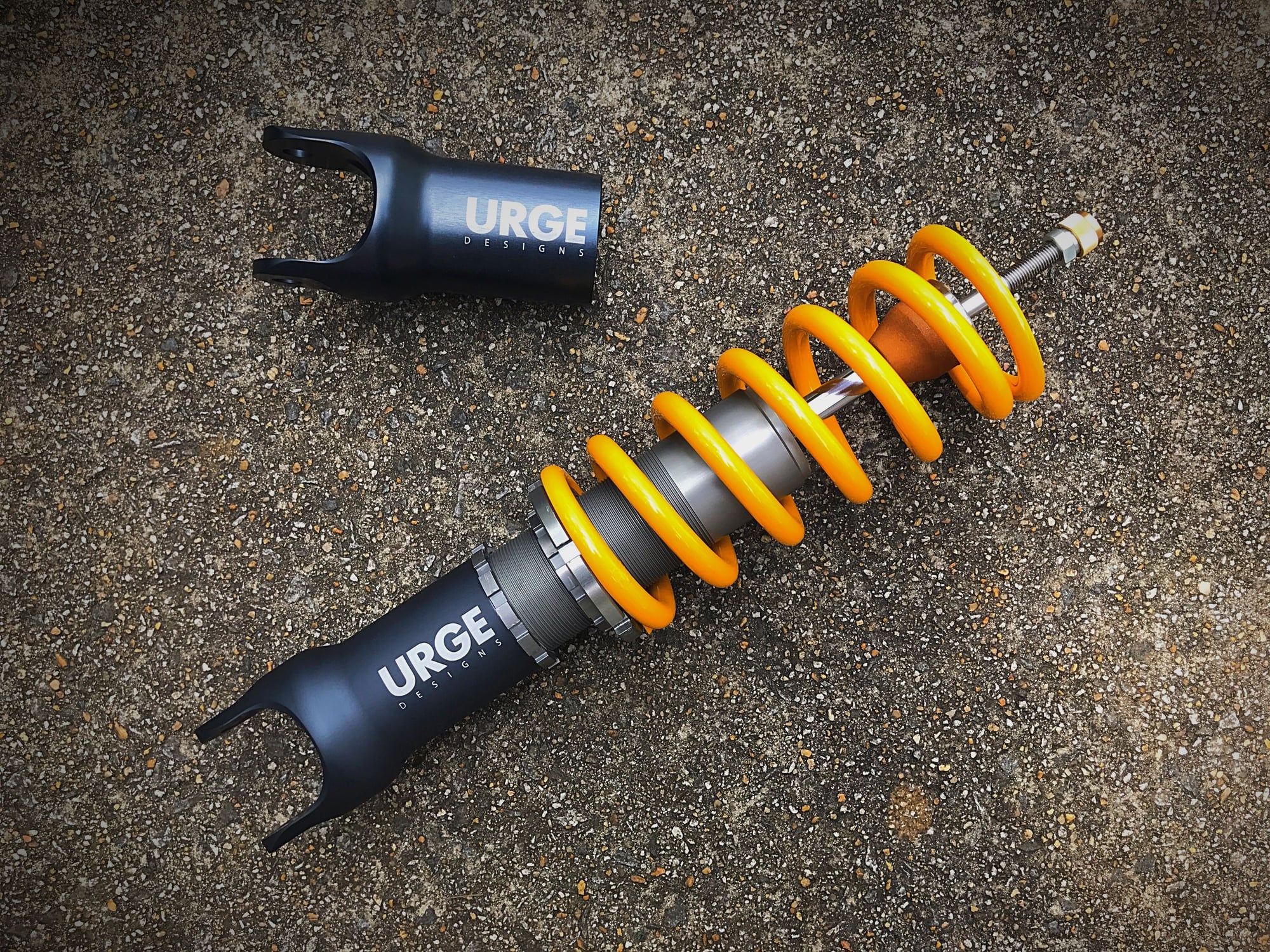
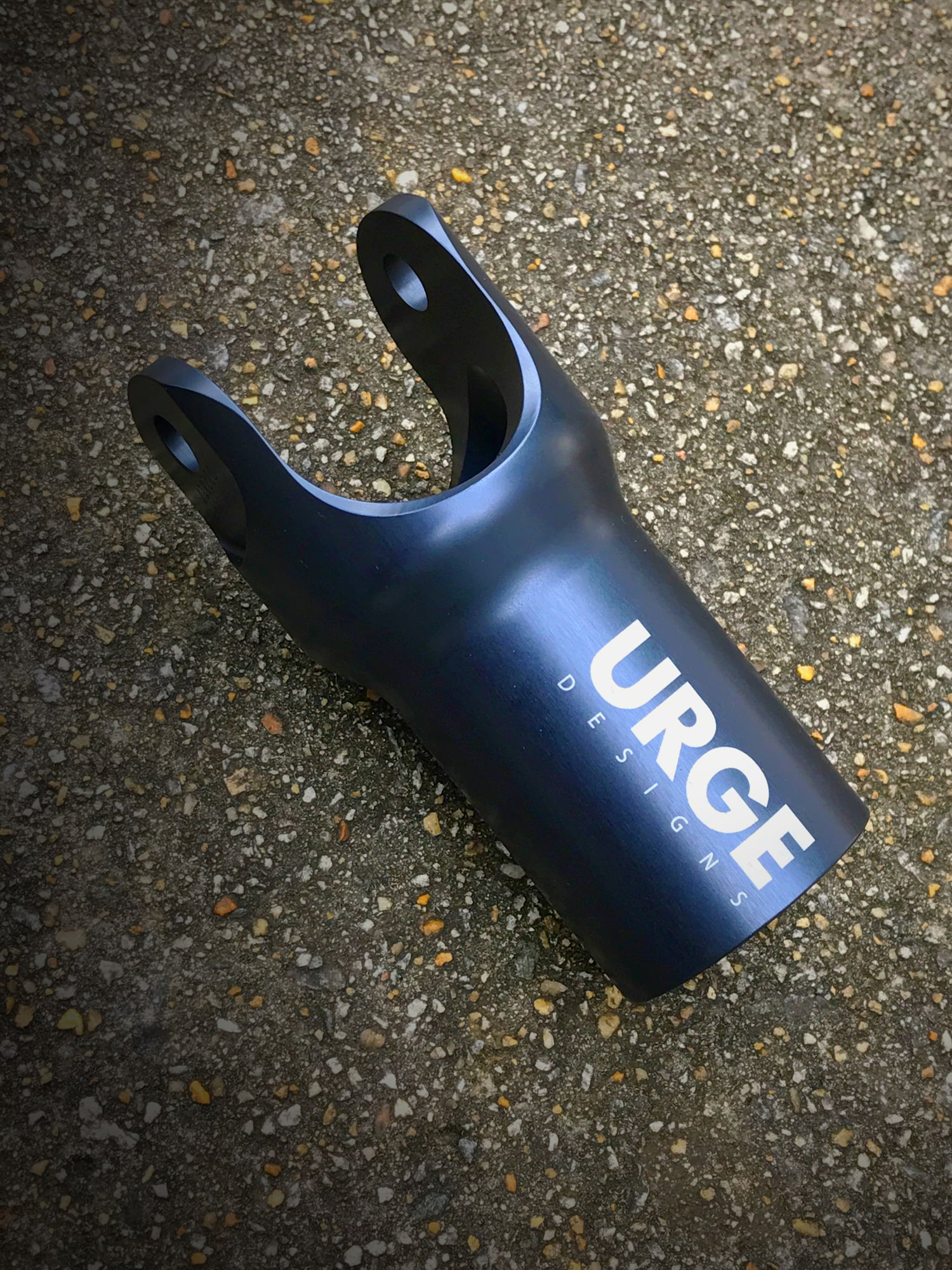
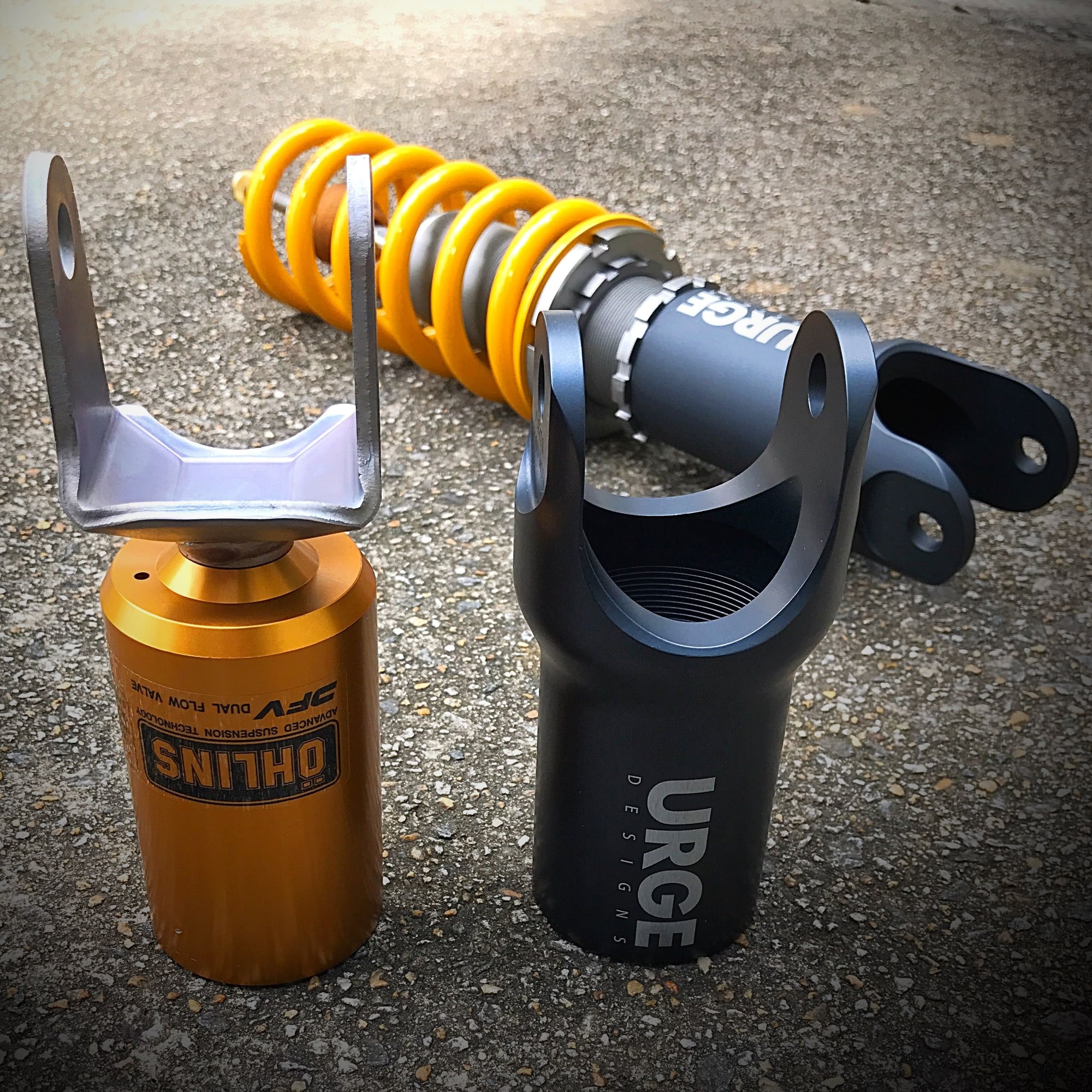